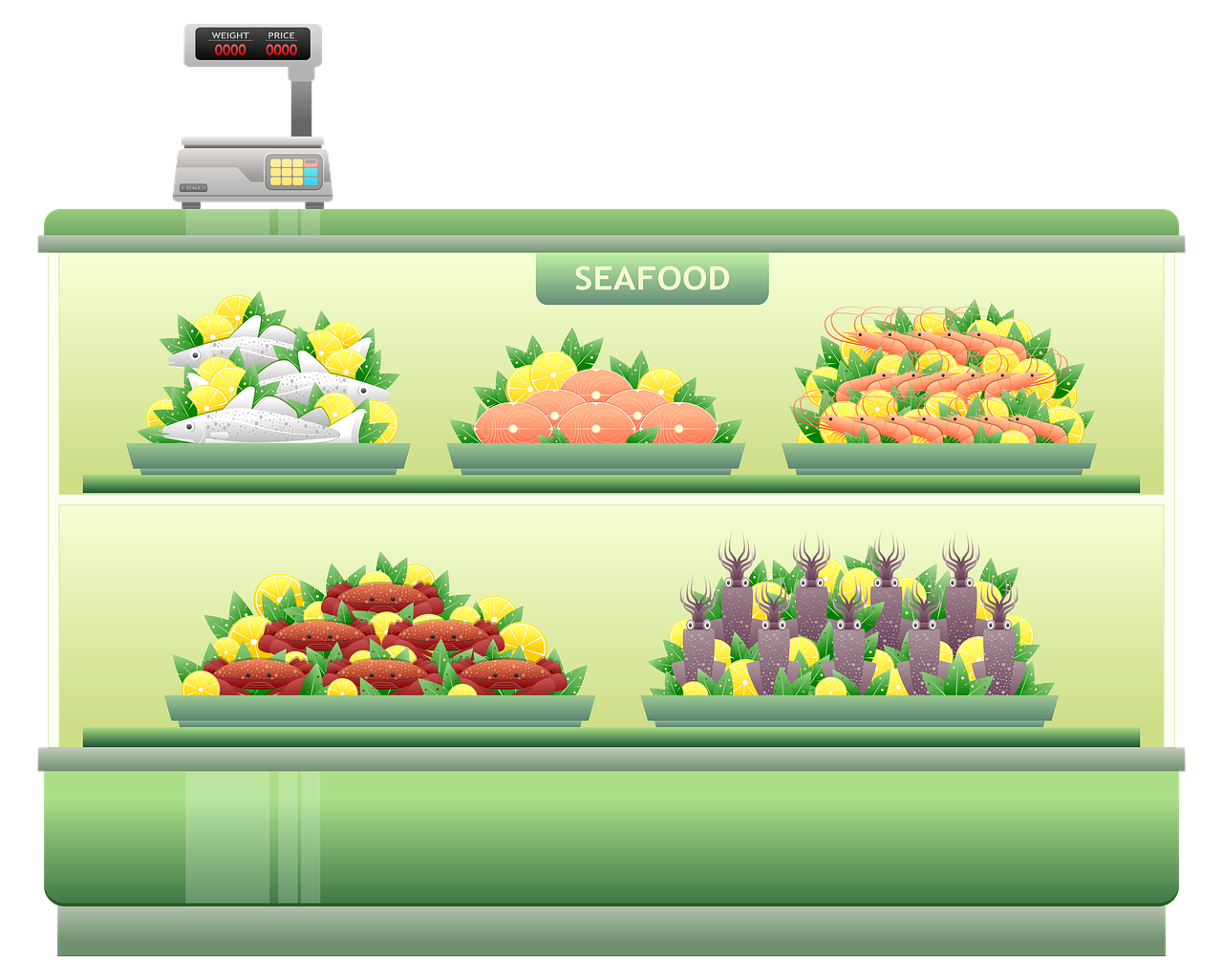
The Truth About Electronic Traceability: Lessons Learned from Working with the Seafood Industry
If you’re reading this, chances are you’ve heard the terms key data elements (KDEs), full chain, traceability, and interoperable; it’s enough to make your head spin. Traceability within the seafood sector is neither new nor novel – companies have been collecting varying levels of product information for decades. Then why are many still stuck using pen and paper? Why does implementing robust data collection practices or electronic traceability still seem so daunting?
FishWise is no stranger to this work. We’ve executed due diligence plans, conducted extensive research, dove deep into supply chains, and worked to implement electronic traceability across our retail partners. From this work, we’ve realized the value of sharing some of the takeaways – the ‘truths’ – behind implementing these kinds of systems. With enough preparation, capacity, and a healthy dose of patience, tackling electronic traceability doesn’t have to be daunting. In the spirit of SALT’s mission to share knowledge with a broader industry audience, FishWise hopes the following ‘truths’ will give you the inside scoop on how to set and manage expectations around implementing an electronic traceability platform.
1. The pre-implementation phase is more important than you think
2. Basic KDEs are still difficult to collect
3. Flexibility vs. standardization
4. Electronic traceability is not a catch-all
5. Constant data verification is essential
Regardless of the realities, the hurdles of implementing electronic traceability systems don’t outweigh the benefits. With these systems, companies not only have access to more timely, accurate, and useful data, but also have increased supply chain transparency. Moreover, these companies are assuming a more proactive role in mitigating sustainability, illegal fishing, and social responsibility risks.